DWD/HER Series
Gas Fired Desiccant Dehumidification Unit
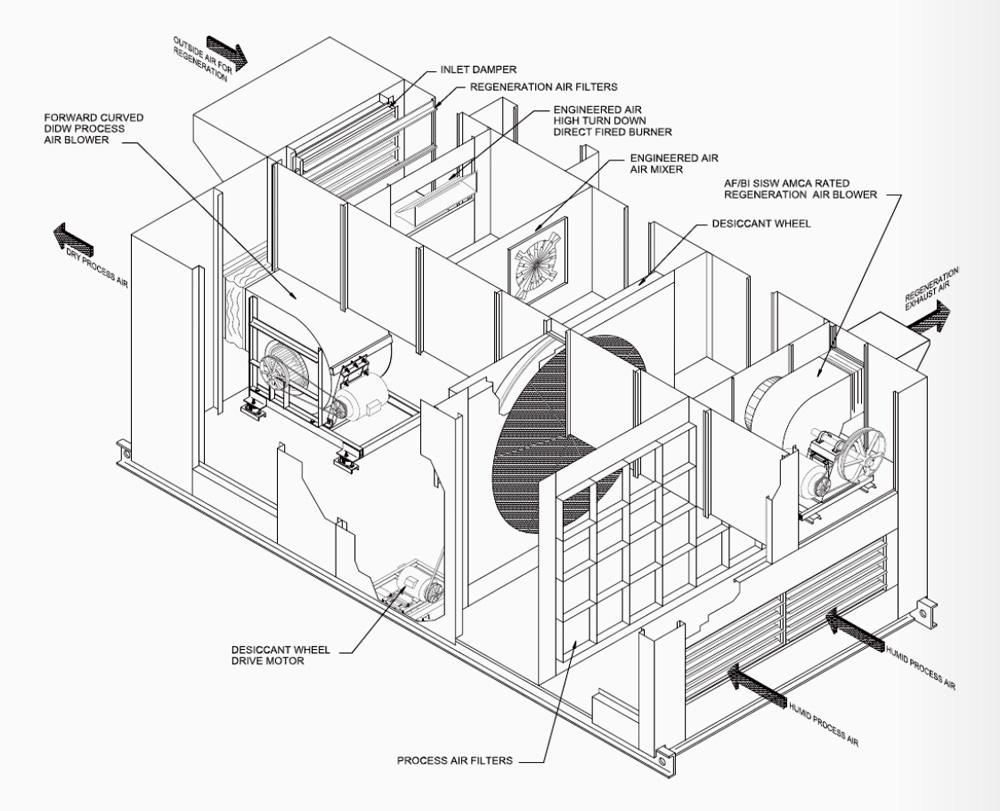
Engineered Air’s DWD/HER Series of fully packaged process / industrial units are ideal for removing moisture in a variety of applications, even in low humidity conditions.
Fundamentals of Operation
The Engineered Air HE/DWD Series gas fired desiccant dehumidifier uses vapor pressure differential to absorb moisture on the relatively cool process air side and then drive this moisture off in the hot regeneration airstream. The process air is hence dehumidified. The desiccant wheel rotates constantly through the process air and the regeneration airstreams. The ambient regeneration air is heated by an Engineered Air direct fired burner (HE Series). The water molecules transferred from the process air are then discharged to the ambient.
Features
- Indoor and outdoor models are available
- 1500 to 15000 CFM process air
- Lightweight, thermally and chemically stable, high performance and low maintenance desiccant wheels using activated silica gel for effective moisture and adsorption even in low humidity conditions.
- Sizes available to dehumidify the process air below 40°F dewpoint and remove up to 470 lb/hr moisture @ 60°F DB / 90%RH
- High efficiency Engineered Air 20:1 high turndown Green Burn direct-fired burner used for desiccant wheel regeneration
- EngA air mixer enhances moisture removal by providing thorough air coverage onto the face of the desiccant wheel
- Dedicated Engineered Air NextGen digital controllers
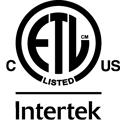
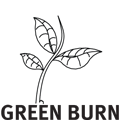
Applications
- Ice rink
- Critical temperature storage such as library archive storage
- Production lines for pharmaceuticals
- Production lines for plastic products
- Dehumidification at fertilizer plants
- Food drying
- Museum
- Environmental test room
- Powder filling applications
Benefits
- Gas fired dehumidification units do not have a DX coil and inherent freezing problems associated with a low temperature DX coil. With mechanical cooling dehumidification, the condensed moisture will freeze on the surface of the evaporating coil when the coil surface is below 32°F as is sometimes necessary to reach low dewpoint levels. As a result, the minimum achievable dewpoint is limited by frosting on the DX coil.
- Lower operating cost — especially in areas where the electricity cost is high and the natural gas cost is low. Mechanical cooling compressors require a significant amount of electricity to provide dehumidification.
- No water condensation issues — the mechanical cooling dehumidification evaporator will condense water which will promote undesired microbial growth in the system.
- Lower maintenance cost — gas fired desiccant dehumidifier has fewer components to service than mechanical cooling dehumidification units.
Optional Features
- Mixing boxes can be provided if required.
- Auxiliary Engineered Air cooling components (FW mechanical cooling or chilled water coil) can be added to re-cool dehumidified process air to neutral condition.
- A sensible heat wheel can be added to re-cool the process air down stream of desiccant wheel and preheat the regeneration air upstream of Engineered Air’s burner.
- High temperature process exhaust heat (approximately 125°F to 280°F) from the building, steam or electric heat, if available, can be used in the regeneration air to reduce the required heating capacity or eliminate the direct fired burner.
- A cooling coil (DX or chilled water) could be used as an option to re-cool the warm dehumidified air.
*Due to continuous product development, specifications, dimensions and capacities are subject to change without notice.