SH Series
Commercial & Industrial Gas Fired Steam Humidifier
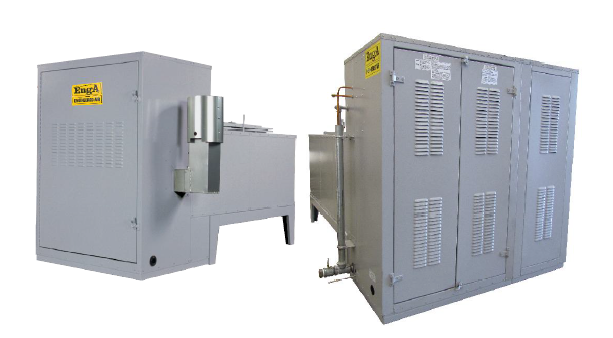
Engineered Air is the proven leader in combustion and heat exchanger technologies. Our high turndown burner and floating, stress relieved heat exchangers have been quality tested for over 25 years of use involving thousands of installations.
Dedicated Engineered Air controls, specifically designed for Engineered Air Burners, are used to achieve up to 15:1 fully modulating turndown ratio. The ability to modulate the combustion process, while maintaining or increasing the efficiency throughout the turn down range, results in the lowest energy cost per pound of steam produced.
This recognized combination of Engineered Air CENCON or BASE controller, burner and heat exchanger is further enhanced to achieve minimum capacity duration at high altitudes.
These proven technologies are the heart of the Engineered Air SH Gas Fired Humidifier.
Related Products
Features
- Up to 650 pounds of steam per hour
- Engineered Air combustion technology
- Up to 15:1 fully modulating turndown ratio
- High efficiency heat exchangers
- Low profile arrangement
- Large tank for less interruption
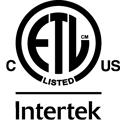
*Due to continuous product development, specifications, dimensions and capacities are subject to change without notice.
Why Humidity?
Control of humidity in a conditioned space plays a major role in providing occupant comfort and in optimizing eletronic equipment performance. Many people, when they think of humidity control, think dehudification, but for a large part of North America, humidity control also means humidification (adding water) during part of the year.
Comfort & Health
Studies have showm that thermal comfort can be achieved at lower temperatures if the humidity levels are maintained at proper levels. Low relative humidity increases evaporation from the skin giving the impression that the air temperature is lower that it actually is. The nose and throat will also see increased levels of evaporating, which can cause drying of the mucous membranes in the respiratory system. All-air systems are particularly sensitive to low humidity levels, because the forced air movement can amplify the effects of evaporation.
While human comfort is maximized between 30% and 60% relative humidity, bacteria, viruses and biological organisms suffer. The influenza virus for example, has the highest mortality rate at 50% RH with its survival rate increasing at higher and lower humidity levels.
Equipment
Operation of electronic equipment may be adversely effected when subjected to relative humidity outside the optimum range for humans. Generally this equipment is designed to operate between 35% and 55% RH. Industrial processes and material storage facilities are also sensitive to humidity. Designers of such applications should be familiar with the effect of humidity on their systems, equipment and materials.
The Structure
When designing a humidification system, the building as a whole must also be considered. Condensed moisture or frost can cause severe damage to surfaces, walls and the structural integrity of the building envelope if not specifically designed and properly protected with vapor barriers. For these reasons, humidity must be properly controlled
Operating Sequence
At the initial start up, the evaporating tank is filled with water to the operating level. On a call for humidification, the modulating power burner is fired in the heat exchanger to provide the required amount of steam. Electronic water level monitoring automatically enables the make up water valve.
The uncontaminated steam generated in the evaporating tank flows through the steam hose or piping to the stream distribution system where the steam is dispersed into the supply air stream.
The humidifier is equipped with fully automatic controls, including auto fill and freeze protection for outdoor installation. The SH Humidifier tank is sized to operate a full working day without a skim or purge cycle. To reduce the buildup of calcium and other minerals, the tank will automatically drain each night and refill the following morning with fresh water
EngA-Sorb Manifold
Engineered Air EngA-Sorb Stainless Steel distributing manifolds are fitted with metering orifices which extend towards the center of the tubes, insuring only the driest steam is injected into the air stream. Each distribution tube is sized for its required steam flow.
It is critical to have a uniform air velocity profile across the steam distribution grid. Air handling applications require the effective distribution grid size to closely match the upstream coil face dimensions. If this is not possible, an adequate transition needs to be incorporated between the coil section and the steam distribution grid. A minimum distance equal absorption or non-wetting distance has to be maintained downstream of the distribution grid before coming into contact with other components.